Australia based Total Marine Technology (TMT) designs and builds vehicles for subsea oil and gas exploration. Its stateof-the-art Remotely Operated Vehicles (ROVs) often perform work at depths of over 1,500 meters. In 2010, TMT landed a five-year, $30 million contract with another Australian company.
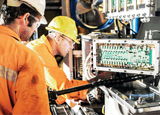
For this specific project, TMT needed to design and build a ROV that could reach depths of over 3,000 meters. For such a task and in order to reach the required depths, only the best in motor starting and electrical equipment would be good enough. When asking for the market’s best choice, the answer spelled ABB.
The challenge
Limited space, high pressure, under water and remotely controlled. Add to that: poor voltage supply. When plunging into the depths with a multi-million dollar, 5,000 kg piece of cutting-edge technology, electrical failures are costly. Harmonic distortions have proven problematic before, resulting in frustrating failures and costly downtime. The low voltage equipment specified has lacked the ability to accommodate the voltage irregularities and coils have burned. A single electrical component failing has often lead to downtime costing much more than all of the low voltage products combined. When building the Typhoon 9, required to reach depths of over 3,000 meters, TMT first had to reconsider its electricalspecifications. TMT contacted ABB.
The solution
The highly polluted power sources, so commonly found on oil rigs, were a problem for TMT. It wanted to ensure its ROVs were fed quality power even at depths of over 3,000 meters. Through a collaborative approach, ABB learned the specific application requirements and was able to satisfy the stringent demands of the subsea environment. ABB in fact delivered all low voltage equipment that TMT needed, from the resilient AF contactors to the space- and energy-saving PSTB softstarter. The result: a more reliable and compact product that also surpassed TMT’s expectations in areas of functionality and cost. It was simply “a market’s best choice”.
ABB AF contactors ensure distinct operation in unstable networks thanks to a wide operating voltage and an electronically controlled coil. Contactor welding arising from voltage fluctuations are eliminated. Furthermore, AF contactors are reliable in very harsh conditions while securing uptime and continuous operation.
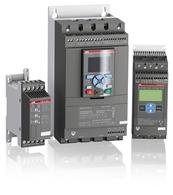