As we all continue hearing about the major benefits of LED technology (also named solid state lighting, SSL) which includes efficiency, long life and reliability. There is a key parameter of LEDs that is often lost or not given due respect into the efficient operation of LED that has a big effect on performance.
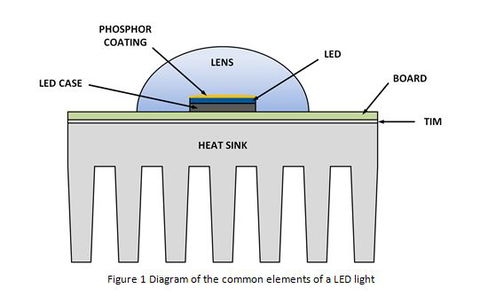
We usually have the perception that LEDs are highly efficient in their conversion of electrical energy into light without generating excessive heat in the process. But in fact between 65 - 85% of the electrical energy generates heat with only the rest actually producing light. We may not feel the high temperatures around the lamp or luminaire due to the small areas of LED chips, but it is definitely present and effects performance.
The impact of the heat generated by LED chips themselves is very high and has negative effects on performance. Whilst LED technology is working towards higher efficiencies in the conversion of energy, quality manufacturers also focus on the best materials, designs and components around the LEDs in order to efficiently dissipate the heat produced.
Understanding LED Components
First of all, I will explain the typical components involved in LED lights and how they work. It is important to understand the function of the components to better understand how thermal management works. The following diagram shows the components of a typical LED chip in a luminaire:
- LED Chip: a LED (Light Emitting Diode) is a semiconductor device that converts electricity into light. It connects 2 types of semiconductor (P-type and N-type) forming a PN junction. When the electric current flows through a LED the charges of the semiconductors recombine and emit energy in the form of photons.
- The LED Case is generally made of plastic and surrounds the LED chip.
- Board: usually a Printed Circuit Board (PCB), it is a substrate on which the LED chip is mounted and soldered. This way the LED is electrically connected to the circuit and also mechanically attached to the rest of components.
- Thermal Interface Material (TIM): adhesive material used to join the LED board to the heat sink, allowing optimal heat transference. It ensures proper contact between the elements for adequate heat flow between the two surfaces. Most common TIMs are epoxy resins and thermal greases.
- Heat Sink: passive heat exchanger made of thermally conductive material, usually aluminium. This is the main element that disperses the heat by means of thermal convection (transferred to the surrounding air) and decreases the temperature of an LED. The design of the fins determines how effectively this heat exchange process is.
- The Lens is usually made of silicone or epoxy resin encapsulating the LED chip. It provides protection and ensures a clear optic for the light source. Being in direct contact with the LED chip the lens has also an important role in the heat management.
- Yellow phosphor coating is added onto the LED chip to produce white light. Typically white light LEDs result from blue light sources filtered through the yellow coating resulting in a white colour.
Not all these components have the primary role of controlling the temperature of the LED, but being so close to the light source, they have relevance.
Then, are those components necessary in a LED light?
The answer is it depends. It depends on the power of that LED, the heat it generates and how well the fixture as a whole can dissipate that heat ensuring an optimal operating temperature. Only by means of accurate designs and conducting thermal management tests, LED lighting manufacturers can determine the elements required to be assembled in conjunction with the LED, their materials and configuration.
We can currently find thousands of different types of LEDs in the lighting market, but the thermal management analysis is the step that makes, in most cases, the difference between a good quality and reliable product and a bad quality one.
What are those negative effects of high-temperature operation in the LED performance?
- Overheating of LED chips causes a reduction of the electrical parameters of the LED: forward voltage VF decreases and so does the forward current IF.
- Reduction of luminous flux (light output) and luminous intensity as a result from changes in the efficiencies of the semiconductor. This is not related to the decrease of forward voltage (VF) as the changes with the temperature are non-linear.
- The lumen maintenance of the LED is accelerated and the lifetime shortened when it continuously operates at high temperatures. We define the lumen maintenance as the operating time in which a LED maintains a percentage of the initial light output, (generally considered 70%, L70).
- Colour shift: some LED lights, based on different colours LEDs (such as RGB, red-green-blue) change their colour when the temperature varies. Some colours are more susceptible to temperature changes than others: amber and red LEDs present a greater colour shift than blue or green LEDs under the same temperature variations.
Some of these effects can be reversible if we operate the LEDs at lower (and optimal) temperatures. But in the long term the lumen maintenance and lifetime of our LEDs may have irreversible consequences when they operate at higher temperatures.
What is the maximum operating temperature of a LED? What establishes the optimal temperature?
The junction temperature Tj determines the maximum operating temperature of the LED’s semiconductor. This temperature is different for every LED chip and is determined by 3 factors:
- the ambient temperature;
- the thermal resistance between the LED and the luminaire’s surrounding components; and
- the power it dissipates during operation
The ambient temperature Ta has a direct impact on the junction temperature: the higher Ta, the higher Tj is.
Thermal resistance is the rise in temperature of a component per unit of power dissipated [°C/W]. Metals typically have low thermal resistance as they are good heat conductors. Air and plastics are poor conductors due to their high thermal resistance.
Hence, the importance of an accurate thermal design and analysis of the elements of the whole luminaire and not just the LED chip itself. Heat must be efficiently and quickly dissipated out of the LEDs to ensure optimal operation. Calculations and analyses must be carried out to find the optimal operating temperature.
The thermal characteristics also have a remarkable impact on the lumen maintenance of LEDs. For a single LED chip the lumen maintenance greatly differs depending on the Tj. The following graph (based upon the IES LM-80-08 standard for LED testing), shows the measured and projected lumen maintenance of one LED at three different junction temperatures.
Figure 3 Lumen maintenance test on a specific LED chip at three different operating temperatures
The same LED operating at a temperature of 105 ˚C experiences a short lumen maintenance, L70 of 22,000 hours approx.; at a lower operating temperature of 85 ˚C, the lumen maintenance almost triples: L70 = 63,000 hours approx.; at an optimal LED temperature of 55 ˚C, the test estimates a L70 above the 200,000 hours.
This is one of the main features of LED light sources evaluated in the IES LM-80-08 standard for testing methodologies.
Conclusion
As we can see LEDs by themselves are not necessarily reliable or efficient products offering many thousands of hours of life. Once the LED chips are manufactured, a profound analysis on thermal management and design must take place for the luminaires in which they will be installed: to encapsulate the LEDs with the adequate components to efficiently release the heat generated and to obtain the best light output from the LEDs even at high ambient temperatures of operation.
In many cases thermal management design and testing is a contributing factor to what sets apart a professional high quality long life LED solution that is fit for use, from an unreliable and untested solution.