Shopping Cart
Distributor Selection
Select the distributor you would like to use for your shopping cart.
Distributor
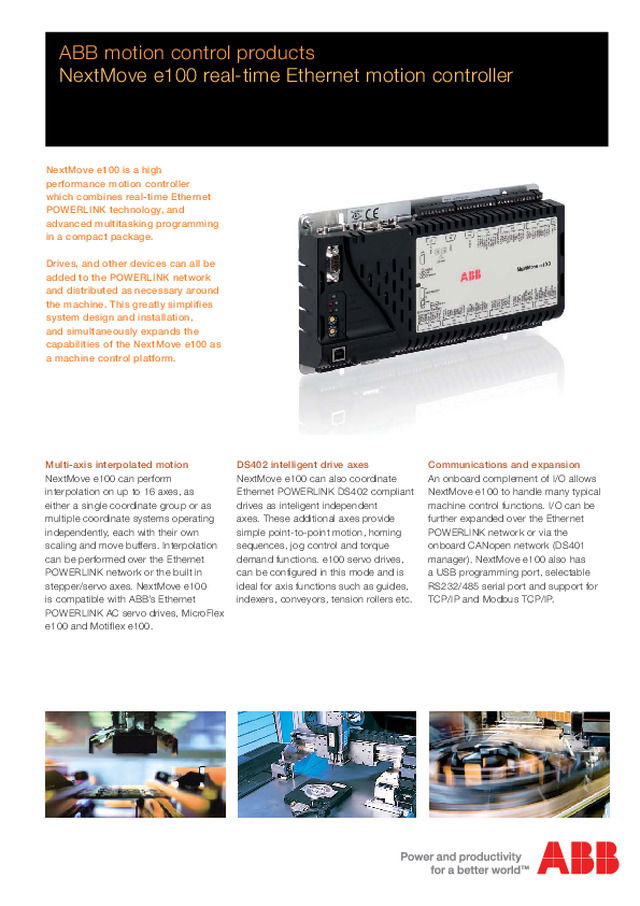
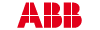
ABB NextMove e100 real-time Ethernet motion controller
ABB motion control products
ABB motion control products NextMove e100 real-time Ethernet motion controller Multi-axis interpolated motion NextMove e100 can perform interpolation on up to 16 axes, as either a single coordinate group or as multiple coordinate systems operating independently, each with their own scaling and move buffers. Interpolation can be performed over the Ethernet POWERLINK network or the built in stepper/servo axes. NextMove e100 is compatible with ABB’s Ethernet POWERLINK AC servo drives, MicroFlex e100 and Motiflex e100. DS402 intelligent drive axes NextMove e100 can also coordinate Ethernet POWERLINK DS402 compliant drives as inteligent independent axes. These additional axes provide simple point-to-point motion, homing sequences, jog control and torque demand functions. e100 servo drives, can be configured in this mode and is ideal for axis functions such as guides, indexers, conveyors, tension rollers etc. Communications and expansion An onboard complement of I/O allows NextMove e100 to handle many typical machine control functions. I/O can be further expanded over the Ethernet POWERLINK network or via the onboard CANopen network (DS401 manager). NextMove e100 also has a USB programming port, selectable RS232/485 serial port and support for TCP/IP and Modbus TCP/IP. NextMove e100 is a high performance motion controller which combines real-time Ethernet POWERLINK technology, and advanced multitasking programming in a compact package. Drives, and other devices can all be added to the POWERLINK network and distributed as necessary around the machine. This greatly simplifies system design and installation, and simultaneously expands the capabilities of the NextMove e100 as a machine control platform.
3AUA0000116020 REV A EN 16.2.2012 #16137 CANopen port - simple expansion − CANopen network manager − System I/O expansion − Communicate with HMI panels − Peer to peer communications Anolog axes - encoder inputs − 3 x incremental encoder inputs − 3 x analog outputs ± 10 V 12-bit − Or use the encoders and analog signals for application purposes separately USB and serial - communications − USB for configuration − Customer PC application interfaces (supported by free ActiveX components) − RS485 serial for PLC, HMI or other device communications. Modbus RTU support Steppers - auxiliary axes − 4 x stepper drive interfaces − Differential or open collector interfaces available (factory order) − A range of stepper motors with integrated drives are available − Linear stepper motors also available Ethernet - POWERLINK and TCP/IP − Network manager or controlled node (CN) − Integrated 2 port hub - ease of connection − Real-time Ethernet performance − Modbus TCP/IP and TCP/IP modes of operation (non real-time) with ActiveX support or RAW Ethernet I/O - digital/analog − 20 x digital inputs (4 fast inputs 1µS latency, ideal for registration functions) − 12 x digital outputs − 1 x relay output − 2 x analog inputs ± 10 V 12-bit − 1 x auxiliary analog output ± 10 V 12-bit MotiFlex e100 and MicroFlex e100 The e100 drive family have integrated Ethernet POWERLINK and provide rotary and linear servo motor control with support for many feedback types such as EnDat 2.2, incremental and SinCos encoders as standard. MotiFlex e100 operates from 180 to 528 V AC three- phase and offers DC bus energy sharing and expansion options including fieldbus systems. MicroFlex e100 operates from single phase 105 to 250 V AC. PC tool offers simple and intuitive commissioning Mint Workbench PC tool offers fast and simple setup, commissioning and monitoring in a single software tool. In addition to a step by step configuration wizard, oscilloscope graphing, parameter view/edit/compare it also includes motion programming, integrated help and a support tool to package a single concise email to streamline technical support when you need it. Powerful machine control ABB’s e100 motion control solutions provide all the benefits of an Ethernet based technology combined with traditional analog, stepper and distributed drives and I/O devices to control an array of different applications. Applications include over-wrappers, vertical form fill seal, tray sealers and markets such as metal forming, material handling and more. For more information please contact your local ABB representative or visit: www.abbmotion.com www.abb.com/drives www.abb.com/drivespartners © Copyright 2012 ABB. All rights reserved. Specifications subject to change without notice.