Shopping Cart
Distributor Selection
Select the distributor you would like to use for your shopping cart.
Distributor

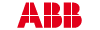
ABB Shutter Control Application Manual
ABB i-bus ® KNX Applikationshandbuch Jalousiesteuerung ABB i-bus ® KNX Application ManualShutter Control
Sample Note Tip Advantage Disadvantage Description of the symbols:
1 Preface/General ...................................................................................................................... 2 1. Introduction 1.1. Selection of the required circuit and control functions .................................................. 5 2. Circuit design 2.1. Switching from one or more positions .............................................................................. 6 2.1.1. ABB i-bus ® KNX push buttons ...................................................................................... 6 2.1.2. Conventional push buttons with binary input ................................................................ 7 2.1.3. Drive control ................................................................................................................ 8 2.1.4. Bus voltage failure, bus voltage recovery, programming ............................................... 14 2.2. Group and central circuits .................................................................................................. 16 2.2.1. Sending two group addresses ...................................................................................... 17 2.2.2. Central telegram and status feedback .......................................................................... 18 3. Control functions 3.1. Timer control ........................................................................................................................ 20 3.1.1. Devices for implementation of the function Time .......................................................... 20 3.1.2. Timer control combined with conditions ....................................................................... 21 3.2. Movement to positions ........................................................................................................ 25 3.2.1. Function Automatic ...................................................................................................... 25 3.2.2. Realisation with standard drives .................................................................................. 26 3.3. Sensor-dependent control .................................................................................................. 29 3.3.1. Weather-dependent control.......................................................................................... 29 3.3.2. Temperature dependent control ................................................................................... 34 3.3.3. Sun position dependent control .................................................................................... 39 Appendix Checklist ............................................................................................................................... 47 Table of contents
2 Preface/General General ABB i-bus ® KNX systems offer an attractive solution which fulfi ls the highest standards in residential, commercial and public buildings. Quality of living, comfort and safety can be easily combined with cost-effectiveness and environmental awareness using ABB i-bus ® KNX systems. The ABB i-bus ® KNX products cover the entire range of applications in buildings: from illumina- tion and blind control to heating, ventilation, energy management, security and surveillance. These demands are can be realised cost-effectively with minimal planning and installation effort using the ABB i-bus ® . Furthermore, the fl exible usage of rooms and the continuous adaptation to changing requirements are simple to realise. Important for the realisation of the elevated demands of building users is however, professional and detailed planning. This application manual – from practical application for practical usage – is intended to assist simpler planning and implementation of a project. Planning of a project One of the main considerations when planning a building control with the ABB i-bus ® KNX is whether the actuators for the circuits are installed on a centralised or distributed basis. Central installation In smaller properties, houses or apartments, all wiring to consumers can be brought to a central point. Distributed installation In a distributed installation the devices are installed in the vicinity of the load. A central installation is more transparent, fewer ABB i-bus ® KNX components are required and the cost per channel is lower. A central installation requires more wiring effort and expense. A distributed installation requires less wiring effort on the load end. A distributed installation signifi cantly increases the cost per channel. The overall system can quickly lose transparency and devices may possibly be diffi cult to access. As the number of ABB i-bus ® KNX devices increases with a distributed installation, the programming effort also increases. Additional power supplies and couplers may be necessary, which will also increase costs.
3 Preface/General Conclusion During planning, it is increasingly signifi cant to consider the constructive features of a building. In practical use, a combination of central and distributed installation has proven to be useful. Distributed installation is not possible, for example, in a dwelling due to space considerations. For larger buildings, a central installation can mean a room, a hall or a fl oor, which still complies with a distributed installation in terms of the overall concept. A further solution for a distributed, room-oriented application are the Room Controller RC/A x.2 and Room Master RM/S x.1 from ABB. For further information refer to the Room Controller and Room Master product manual. ABB i-bus ® KNX application manual Shutter Control All the possible circuit confi gurations are explained after a brief introduction in this application manual, e.g. operation from one or more points. The many application examples are comple- mented by information, tips, benefi ts and disadvantages which offer a quick and simple insight into the advantages of the different control functions, e.g. timer control, sensor-dependent control. The selection possibilities of the individual control functions and their combination possibilities are very comprehensive. The checklist from ABB has proven to be very useful for simplifi cation of the engineering involved. A checklist template can be found in the Appendix. The application manual is intended for persons who already have acquired basic knowledge in ABB i-bus ® KNX (basic functions, topology, addressing, …), e.g. in a certifi ed ABB i-bus ® KNX training session.
4 1. Introduction The control of motor drives is one of the main applications of the ABB i-bus ® KNX. The following applications can be operated with motor drives: – Blinds with and without louvres, e.g. in commercial buildings such as offi ces, hospitals, schools – Roller blinds, e.g. like in dwellings – Electrically operated windows – Skylights, e.g. in factory halls – Electrically operated curtains – Doors, e.g. garage doors – Awnings – Partitions – Ventilation fl aps Up to now, only on-site operation of drives was possible in most cases. This makes the use of additional functions such as wind monitoring devices or central/group controls more diffi cult. The implementation of such functions can only be undertaken with a lot of effort and was expensive for this reason. Implementation is not a problem with the ABB i-bus ® KNX. There is complete fl exibility for the following : – On-site control – Group/central operation – UP/DOWN functions – STOP functions – Louvre adjustment – Move to position – Safety monitoring, e.g. with weather sensors – Timer control, e.g. with absence of the occupants – Inhibiting/interlocking a drive – Automatic function Automatic shading should be implemented in a school so that lessons are not interrupted. However, darkening of each individual classroom must still be possible when required, e.g. when showing a fi lm or beamer presentation. Important preliminary considerations of such a project have proven useful for optimum planning of a project. This includes selection of the circuit and control functions. Introduction
5 1.1. Selection of the required circuit and control functions The blind and roller blind control with ABB i-bus ® KNX is characterised by a high level of fl exi- bility. This includes a large range of individual control functions and their combination possibi- lities. The following functions are available: Circuit design – Switching from one or more positions – Central and group switching Control functions – Timer control • Devices for implementing the function Time • Timer control combined with conditions – Movement to positions • Automatic function • Realisation with standard drives – Sensor-dependent control • Weather • Temperature • Sun position Introduction
6 Circuit design 2. Circuit design To plan a useful circuit design, the different circuit confi gurations must be reviewed in the preliminary considerations and then selected appropriately: – Switching of one or more positions – Central and group switching 2.1. Switching of one or more positions Even with the use of intelligent electrical installation systems such as ABB i-bus ® KNX, the basic functions for every application with blind actuators incorporate local operation of one or more drives using push buttons. These are generally tried-and-tested and proven in practi- ce. 2.1.1. ABB i-bus ® KNX push buttons With this solution, the functions are implemented with both sides of the ABB i-bus ® KNX push button, i.e. one end is used for UP and the other is used for DOWN. Both ends enable the STOP function and the louvre adjustment. The blinds in a conference room should be moved as required. One or more drives are operated using a local button. The following principle has proven itself in practice: – Long button push: the blind moves UP, a logical 0 is sent, or DOWN and a logical 1 is sent (1 bit telegram). – Short button push: the blind stops (1 bit telegram). – Repeated short button push after the STOP telegram: the blind moves in steps or the louvers are adju- sted. The operating principle can be implemented with ABB i-bus ® KNX bus push buttons or with conventional push buttons in conjunction with a binary input.
7 Circuit design 2.1.2 Conventional push buttons with binary input If a Binary Input is used, e.g. US/U x.x or BE/S x.x, it is possible to operate with just a single input and one push button. Here an alternate long button push operates the UP/DOWN func- tion and a short button push the STOP function or louvre adjustment. Fig. 1: Parameter window Shutter sensor of the binary input Only one channel and push button are required. The parameterisation offers a high level of fl exibility. You can also connect (rotary) switches. If the blind is in the middle position, it is not clear beforehand the direction in which the blind will move after a long button push. This type of operation is unconventional for blinds. – Sending a 1 bit telegram with the value 0 for UP, or the value 1 for DOWN is defi ned in the ABB i-bus ® KNX and should be observed with central telegrams. – The assignment of the functions for short and long operation as described above has proven useful in practice. The functions can be swapped as both telegrams are 1 bit telegrams. – The functions behind the short and long operation can be assigned on two different push buttons. This is not implemented for economy reasons with room buttons (double the number of push buttons), but is frequently used in control panels or LCD displays. – The group addresses of these functions, move UP/DOWN, STOP or louvre adjustment are different!
8 Circuit design 2.1.3. Drive control The drives are controlled by a changeover contact in the blind actuator. The corresponding winding in the drive is controlled to comply with the direction of motion. It is not possible to activate both drive windings simultaneously. This would cause the destruction of the drive. Fig. 2: Connection schematic ABB i-bus ® KNX Shutter Actuator JA/S 4.230.1 There are conventional actuators which can be programmed as a Switch Actuator or a Shutter Actuator. When used as a blind output, two relays are used which are mutually exclusive using software. A mechanical interlock is not available which in the most unfavourable cases, e.g. with a software problem, can cause damage to the motor. In the parameters of the Shutter Actuators, e.g. MDRC devices JA/S x.x or modules of the Room Controller JA/M 2.x.1, it is still possible to make every channel a switch channel. Here, only one end of the changeover contact is used, see Fig. 3. The number of parameters is reduced using software so that it fi ts classical switching functions, e.g. ventilation fl aps or lights. L PE N L N M M M M JA/S 4.230.1 A C B D L L μ μ
9 Circuit design The following circuit shows the switch actuator function using the ventilation fl ap connection as an example: Fig. 3: Connection schematic ABB i-bus ® KNX Shutter Actuator JA/S 4.230.1 with switch actuator/ventilation fl ap function The shutter actuators have 6 A relays installed which are practically always suffi cient for the drives which are to be connected. For further information see Parallel connection of several drives, chapter 2.1.3.4. L1 L2 PE N 2 N M M M M JA/S 4.230.1 A C B D L L Unlike switch actuators and lamps, several loads (drives) will not be connected in parallel to the channels of the shutter actuators. If a drive was still operating and the other was already in its end position and switched off via an end limit switch, reverse voltage will occur on the drive with a danger of damage. If this type of installation is still demanded, operation with isolating relays is required.
10 Circuit design 2.1.3.1. DC drives In addition to 230 V AC drives, there are also DC drives. Their area of application is with electrically operated windows and internal blinds. On DC drives, the direction of operation is reversed by changing the polarity on the drive. In principle, the respective actuators function exactly as with the AC drives, see Fig. 4. The application software is also the same. The DC voltage supply is applied externally. The shutter actuator permits a voltage between 12 and 48 V. Fig. 4: Connection schematic ABB Shutter Actuator JA/S 4.24.1 with DC motors 2.1.3.2. Reversal time or Pause on change in direction An important parameter in the shutter actuators is the so-called reversal time. It defi nes how long the drive remains stationary when moving in one direction after a telegram to move in the other direction is received. –+ M – M – M – M – JA/S 4.24.1 A C B D This time is important for the protection of the motor or the connected mechanical components. The default value is 500 ms and should be corrected if necessary after consulting the manufacturer of the drive.
11 Circuit design 2.1.3.3. End limit stop Blind drives feature an end limit stop in the housing. If the drive reaches the end position at the top or bottom and with closed or opened windows, the drive must be stopped. The drive is disconnected from the voltage supply. This is achieved using end limit switches. There are two possibilities for an end limit stop: – Mechanical end limit switches – End limit stop via overcurrent or undercurrent Mechanical end limit switches The drive operates the blind until the respective end limit position is reached. The circuit is interrupted here. End limit stop via overcurrent or undercurrent With an end limit stop initiated by overcurrent or undercurrent, the drive moves to the respective end position and is mechanically blocked. The resulting increase (drive in upper end position) or reduction in current (drive in lower end position) is detected and switch off is initiated. The motor also switches off when an obstacle is detected. The drive and the shutters to be controlled must be matched to one another, i.e. correctly confi gured. Otherwise the drive will not operate correctly, i.e. the shutter may stop in the middle or too late in the end position. This can damage the shutter. To guarantee an exact position feedback of the shutters, (also refer to chapter 3.2 Positioning) the travel time of the shutter must be entered for the Shutter Actuator in the application. After the travel time has elapsed, the changeover contact is switched to a no-voltage state. Using a further parameter, the time for shut down can be selected to be longer than the real run time, ensuring the drive reaches the end positions even under unfavourable conditions. End limit position switch off is mandatory. The isolation of the relay in the Shutter Actuator is only an additional protective measure.
12 Circuit design 2.1.3.4. Parallel connection of several drives Normally only one drive is connected per channel, otherwise reverse voltages may occur with the parallel connection of several drives to a channel. Background: Fig. 5: Source: Berker Both drives are controlled in the same direction of operation when the switch is actuated. When drive 1 has reached the end position, end position switch E2 opens. Drive 2 is still in operation and puts drive 1 back into operation moving in the opposite direction via a reverse voltage on its capacitor. Thus E2 is closed again after a short time. As a result, drive 1 again operates in the original direction of motion until contact E2 is reopened. These switching processes can be recognised by oscillation of the blinds. As the reverse voltage can be up to 1000 V and many changes of direction occur over a short time, end position switch E2 is overloaded. This irrevocably leads to welding of the contacts. Accordingly the end limit stop is put out of operation in this direction of movement. The result: destruction of the motor and/or the blind. Should parallel installation be required however, it can be implemented in two ways: – Use of isolating relays – Shutter Actuator JA/S 2.230.1 Use of isolating relays Isolating relays are used between the motors and the changeover contacts of the Shutter Actuator and electrically isolate the motors from one another, so that there are no problems caused by reverse voltages. There is increased installation and wiring effort which leads to higher costs.
13 Circuit design Shutter Actuator JA/S 2.230.1 One exception is the use of the Shutter Actuator JA/S 2.230.1. It allows for the connection of two drives to a single channel. These are of course internally isolated by an isolating relay. Fig. 6 L PE N L N M M M M JA/S 2.230.1 B A L L Both drives on channel A or B run in parallel and cannot be operated separately. This fact must be considered in the planning stage. This solution is often used to save costs. An alternative here is the use of the Shutter Actuator RA/S 4.230.1, a 4-channel device. The difference to the other Shutter Actuators is the reduced software functionality features: – UP/DOWN – STOP – Louvre adjustment – Wind monitor function The price of the 2 x 2-fold Shutter Actuator JA/S 2.230.1 and the Shutter Actuator RA/S 4.230.1 is practically the same.
14 Circuit design 2.1.4. Bus voltage failure, bus voltage recovery, programming To prevent uncontrolled movement or stopping at bus voltage failure, bus voltage recovery or programming, there are many setting options in the ETS with the Shutter Actuator JA/S x.x and with the Shutter Actuator Module of the Room Controller. Fig. 7 No reaction here means that this telegram is executed up until the end, e.g. when the drive is operating. No position can be set with bus voltage failure. 2.1.4.1. Status messages Unlike switchable illumination (simply ON or OFF), the motion of drives is a dynamic process. Therefore it is frequently interesting to receive status messages with blinds. The following mes- sages are available for each channel: – Position (blind height and position of the louvres, each are a 1 byte telegram) – End limit position reached (1 bit, both for top or bottom) – Manual operation Additionally, a status byte is available, which will inform you whether functions Automatic or Safety are present.
15 Circuit design Standard Motor Interface (SMI) With the use of conventionally available Shutter Actuators and drives, it is not possible to receive feedback messages directly from the drive, e.g. the position or faults. This fact changes with the use of intelligent drives which can communicate with the actuator. A standard for this approach is characterised by the use of the Standard Motor Interface (SMI). ABB already has a ABB i-bus ® KNX Shutter Actuator for SMI motors, the JA/S 4.SMI.1M. Fig. 8: Shutter Actuator JA/S 4.SMI.1M and connection schematic For further information see www.smi-group.com and manual JA/S 4.SMI.1M L L N N A B I + C D I - I + I - I + I - I + I - max. 4 x SMI U S U S A B C D Man. JA/S 4.SMI.1M A A A A JA/S JA S S 4 4 A A A A/S A/S B B B .SMI SM II.1M .1M B B B MI MI C C C D D D M M M M M M a a n n n. L1L2L3 PE N N L 12 E N 3 N max. 4 x SMI
16 Circuit design 2.2 Group and central circuits A very important function of the ABB i-bus ® KNX systems is the realisation of group and central circuits. Here the complete building, a fl oor, or an area composed of a combination of func- tions can be switched from one or more locations. Using conventional methods, the realisation would require considerable additional installation time and expense. Using the ABB i-bus ® KNX this is simply possible using the respective programming. Fig. 9: Push button for shading on the control panel of the Edison training room at ABB If all external blinds are open, and all internal curtains are to close simultaneously in an offi ce building via a central telegram, a group address with logical 0 for Open blinds and a logical 1 for Close blinds must be sent. There are different possibilities available for implementation: – Move the Shutter Actuator via the Position function, see chapter 3.2 Positions – By inverting the value of a group address, e.g. with the Logic Module LM/S 1.1 or Appli- cation Unit ABL/S 2.1 – By sending two group addresses with a push button 1. In a dwelling, all roller blinds in the living room, all drives on the ground fl oor as well as all roller blinds in the house can be controlled via push buttons. 2. The shading of an offi ce building is retracted every evening; the facade of the building has a uniform appearance. 3. The caretaker of a school can centrally raise or lower the shading of each individual classroom using a visualisation system. With a central telegram for drives, a separate push button is confi gured for both UP/DOWN telegrams. A TOGGLE push button is not useful here, as it is unclear which telegram is executed next. A free fi eld of vision to the shading may also not exist.
17 Circuit design 2.2.1. Sending two group addresses Sending two group addresses is possible, when a group address is sent on the rising edge, when a push button is pressed as well as on the falling edge when the push button is released. Both addresses can contain different values. Devices already featuring this capability are the Binary Inputs BE/S x.x. Fig. 10: Parameter settings of the binary input The Busch-triton ® switch sensor or the inputs (e.g. BE/S x.x and US/U x.2) with the function 1 bit light scene also enable this function, where two actuator group types use 1 bit with the presetting ON or OFF. Further information about the function Scene can be found in the application manual Lighting.
18 Circuit design Fig. 11: Parameter settings of the Universal Interface US/S x.2 2.2.2. Central telegram and status feedback The description of the available status messages with Shutter Actuators are described in chapter 2.1.4.1 Status messages. It is important to observe the telegram traffi c caused by status feed- back messages of the individual drives during the implementation of a central group address. In an offi ce building with twin-face-facade, all windows are electrically operated via the ABB i-bus ® KNX. This telegram is implemented via a visualisation system. All drives practically move at the same time and report by telegram when they have reached their fi nal positions, e.g. closed, not closed, maybe their position also. This is also shown in the visualisation UP, DOWN, system. A corresponding communication object is available in the Shutter Actuators JA/S x.x. The consequence is that the quantity of both line and area telegrams will dramatically increase on the bus. This approach will lead to an increased bus load and may even cause an overload which will result in the loss of data where the states of the windows are not correctly represented. In order to avoid a possible overload of the bus, the central telegram is staggered, e.g. telegram is implemented by storey or facade. Staggered sending is easily implemented with the Application Unit ABL/S 2.1.
19 Fig. 12: Central blind control with Application Unit ABL/S 2.1 When triggering the telegram via the group address 8/0/7, the west facade moves fi rst, followed 20 s later by the south facade, another 20 s later by the east facade and fi nally the north facade with a total delay of one minute. The can be subdivided even more if required with the objective of sending the feedback telegrams on the bus at different times. The outputs should be parameterised so that a new value of the communication object sends this value. This ensures that if an identical motion telegram is received a number of times, e.g. move UP, it will also be undertaken a number of times. Circuit design
20 Control functions 3. Control functions The following control functions are available to operate the shading, windows, skylights and awnings of a building as comfortably as possible: – Timer control – Movement to positions – Sensor-dependent control Weather-dependent control Temperature dependent control Sun position-dependent control 3.1. Timer control Timer control is an interesting application for electric drives as it allows determined drives to be operated automatically as a time-dependent function. In addition to the classic possibilities offered by timer control, this may also be combined with different conditions. 3.1.1. Devices for implementation of the function Time With a bus system such as the ABB i-bus ® KNX it is easy to control the timer with a central time control clock. 1. In a dwelling the blinds should be raised every morning at 8 a.m. and lowered in the evening at 8 p.m. 2. In an offi ce building the sun screen should be lowered in the evening after the offi ce closes. The switch actuators alone do not provide the possibility of switching at certain times. This would be too complex as each device would require its own timer (quartz). Possible devices for realisation of a timer control are: – Classic ABB i-bus ® KNX clocks with 2 … 4 channels – LCD Display MT701 – Controlpanel and Busch-ComfortTouch ® panels – Application Unit ABZ/S 2.1 with application Times/Quantities – Visualisation software
21 Control functions Fig. 13: Overview ABB i-bus ® KNX devices with function Time For further information see the application manual Lighting and lighting control, Devices for implementation of the function Time 3.1.2. Timer control combined with conditions In addition to the timer control, linking to different conditions is possible: – External brightness – Presence of persons These functions can be implemented with additional intelligence such as the Application Unit ABL/S 2.1 or the Logic Module LM/S 1.1. The functions Safety and Automatic are the excep- tion, e.g. wind and rain. These already have a high priority in the Shutter Actuator and always have a higher priority for safety reasons. No external logic except the parameter settings in the Shutter Actuator is required. For further information see chapter 3.3 Sensor-dependent controls e.g. FW/S 4.5 1 bit, 8 bit Date, time (3 bytes) Date, time Date and time can be received from (3 bytes) another KNX clock or transferred to there (data format 3 bytes) 1 bit, 8 bit At the set times the 1 bit switching telegram or the 8 bit value telegram are sent ABZ/S 2.1 1 bit, 8 bit Date, time (3 bytes) Busch-ComfortTouch ® bzw. Controlpanel 1 bit, 8 bit Date, time (3 bytes) MT/701.2 1 bit, 8 bit Date, time (3 bytes) PC with visualisation 1 bit, 8 bit
22 Control functions 3.1.2.1. Linking with external brightness Solution with Application Unit ABL/S 2.1 For the closing movement, the operating push button with group address 0/0/3 enables the func- tion with a logical 1. The clock and the Brightness sensor send a logical 1 in the evening. The drive closes the blinds if both conditions are fulfi lled; AND condition: dark and 8 p.m. Fig. 14: Logic for closing movement For the opening movement, the operating push button with group address 0/0/3 enables the function with a logical 1. The clock and the light evaluation switch send a logical 0 in the mor- ning. The drive opens the blinds if both conditions are fulfi lled; OR condition for logical 0: bright and 8 p.m. The blinds in a dwelling should be raised every morning at 8 a.m. and lowered in the evening at 8 p.m. The external brightness should also be considered, This means that the blinds open at 8 a.m. in the mor- ning, provided that it is bright outside and close at 8 p.m. in the evening, provided that it is dark outside. Logical 1 lowers, logical 0 raises the shutters. The timer only has the function of setting a 0 fi lter, i.e. a logical 0 and as a result the UP telegram is inhibited. The parameter settings must be observed. The output sends on each calculation.
23 Control functions Fig. 15: Logic for opening movement Both states must be 0. Only in this way is the result of the operation a logical 0 and the drive operates to open the shutters. The timer only has the function of setting a 1 fi lter, i.e. logical 1 and consequently to inhibit a move DOWN telegram. The parameter settings must be observed. The output sends on each calculation. If the input signal is stored in all gates during the inhibit phase, after the function is enabled using the enable button, the original motion telegram is executed retrospectively.
24 Control functions 3.1.2.2. Link with presence of persons Solution with Application Unit ABL/S2.1 or Logic Module LM/S 1.1 Just one gate is suffi cient to implement this function. The clock sends a telegram with the address 0/0/5 and the value 1 at 5 p.m. The presence detector disables the telegram of the timer with a detected presence via the control input or enables it when no presence is detected. By setting the parameter Save during blocking phase, the drive closes if the room is unoccupied later than 5 p.m. Fig. 16: Logic with Application Unit ABL/S 2.1 The shading of an offi ce building closes in the evening after the offi ce closes. Presence detectors also de- tect whether there are persons located in the rooms. Using linked conditions, the shading only closes at 5 p.m. in rooms which are not occupied. The shading of the other rooms only automatically closes when persons have left those rooms.
25 Control functions 3.2. Movement to positions Movement to a position is a signifi cant function in the area of motor operated applications in the fi eld of building automation. This function is available in all MDRC Shutter Actuators JA/S x.x as well as in Shutter Actuator Module JA/M of the Room Controller. 3.2.1. Function Automatic Using the function Automatic, it is unnecessary for the user to set these positions manually on-site. The function Positioning is comparable with a scene. For further information see application manual Lighting and lighting control, Scene The communication between the sensor which recalls or stores the position and the Shuter Actuator is via a 1 bit telegram. In this way every sensor can be used without additional devices. Fig. 17: Shutter Actuator with the function Positioning 1. The shading of a public building moves to a shutter height of 50 % when a button is pressed in the room. In this manner, the sun does not shine directly into the room, will not dazzle the occupants and natural light still permeates the room. 2. Louvres are installed in a conservatory to protect against the sun. A brightness sensor detects the external brightness. When a certain value is exceeded, the shutters move down by 80 % and the louvres close up to 75 %. Electrically operated windows are installed in the upper third of the glazed facade of an offi ce building. The window opens via a push button in the room. The windows can move to three positions dependent on the wind speeds. This function Automatic offers a high level of comfort and is economic. The heat irradiation from the sun is reduced and a diffused external lighting source is still provided. Call position Save position Shutter Actuator Push button Move to position (height and louvre angle)
26 Control functions Fig. 18: ABB i-bus ® KNX push button with 4 rockers 3.2.2. Realisation with standard drives Conventional standard drives in the fi eld of intelligent installations have no option for position feedback. For this reason the drive is moved over time, i.e. the run time is measured when the drive moves. Important here is a knowledge of the total travel time. In this way the drive can be positioned accordingly. There are two possibilities for positioning: 1. Indirect positioning 2. Direct positioning It is possible to defi ne a position via the parameters of the Shutter Actuator, as well as to save the setting of a modifi ed position. Using a ABB i-bus ® KNX push button two positions should be recalled and stored. Using the left rocker, switch position 1 is recalled with a short button push and stored with a long button push. Using the right rocker switch, position 2 is recalled with a short button push and stored with a long button push. The software function Shutter is used with the push buttons. This can differentiate between long and short button actuation. Using a further rocker switch of the ABB i-bus ® KNX push button, normal UP/DOWN, stop and possibly even louvre adjustment can be operated. Shutter Light TV Light Position I 0 1 2 1 2 Short button push:Move to position 1 Long button push:Save position 1 Short button push:Move to position 2 Long button push:Save position 2 Shutter DOWN/STOP Shutter UP/STOP
27 Control functions 3.2.2.1. Indirect positioning With earlier shutter actuators it was necessary to move to the end limit position – either the upper or lower position – before every positioning motion. From this defi ned position the drive is then moved over time to the actual desired position. 3.2.2.2. Direct positioning Today, direct positioning of the drive can move from any position directly to the next. Travel time Important is the entry of the total travel time of the drive from top to bottom or from bottom to top. This ensures that the highest possible accuracy is achieved. As it is not possible to distinguish between upward and downward motion, the mean value of both times is used. Practical application has shown that there is a slight difference between both times. The run times should be determined by measurement and entered in the parameters of the Shutter Actuator. If an upper or lower end position is reached, the timer is again set to zero. Indirect positioning can also be set on the Shutter Actuators with positioning for reasons of compatibility with older components. Should you only move between the positions without ever reaching an end limit, there is a danger of inaccuracy. This case will practically never occur in practice. If this is the case however, reference run Movement to the end limit can be activated via a ABB i-bus ® KNX telegram. In an offi ce building a reference run should be undertaken at least twice a day to ensure the highest possible level of accuracy. The reference run is initiated using a timer program before work starts at 6:45 a.m. and during lunch break at 12:45 p.m. These times have been selected to run this function out- side of normal working hours. The reference run is ended when the drives return to the original position. This can be set in the parameters, it ensures that the previous state is re-established.
28 Control functions Positioning of the louvres In addition to the blind height, the louvres can also be moved to a defi ned angle. As in Chapter 2.1 Switching of one or more positions, the louvre positioning is achieved by stepwise motion of the drive. Fig. 19: Stepwise motion of the louvre adjustment Louvre adjustment with MDRC Shutter Actuator JA/S x.x With the MDRC Shutter Actuators JA/S x.x, the switch on duration of the louvre adjustment and the number of stages from fully closed to fully open can be set. The shorter the switch-on duration, the more exact the positioning. The number of steps must be deduced by testing. Louvre adjustment with the Shutter Actuator Module of the Room Controller RC/A x.2 With the Shutter Actuator Module of the Room Controller RC/A x.2, the total motion time of the Louvre adjustment is parameterised. The number of louvre steps is also determined here. Multiplied with the switch-on duration, this results in the overall motion time of the Louvre adjustment. 3.2.2.3. Implementation with intelligent drives Intelligent SMI drives where there is a direct position feedback have only recently become available. For further information see chapter 2.1.4.1 Status messages or www.smi-group.com 1st button push for louvre adjustment 2st button push for louvre adjustment Motor voltage Louvre adjustment time Time If the drive is blocked, e.g. shutter has frozen in place or there is an obstacle, it is not possible to detect this from the Shutter Actuator due to a lack of status feedback. There is an undefi ned relation between the position of the drive and the detected time. After removal of the block and movement to the end limit position, the position is once again clear and the timer is reset to 0.
29 Control functions 3.3. Sensor-dependent control Sensor dependent control is a very important function in the fi eld of intelligent installations. This functionality is contained in the software of the Shutter Actuator and serves the needs of safety, economy and comfort. A differentiation is made between: – Weather-dependent control – Temperature dependent control – Sun position-dependent control 3.3.1. Weather-dependent control The forces of nature act directly on an external blind or sun screen. These forces can be dama- ging for the shutter, blinds or the drive: – Wind, e.g. damage to the sun screen – Rain, e.g. the sun screen or the awning made of fabric may not become wet; there is a danger of damage from mildew – Frost, e.g. the service life of the fabric is reduced and there is a danger that all mechanical parts will freeze solid, e.g. in the guide rails Safety-relevant sensors are very important even with electrically operated windows and skylights: – Wind, there is a danger of wind damage to the window, e.g. due to the sail effect – Rain, ingress of water in the building Changes in the weather can be detected by safety-relevant sensors from ABB and the drive (e.g. sun screen) can be controlled as required. The response to the weather is set directly in the Shutter Actuators. The sun screen in a school should be moved to a predetermined position if a defi ned brightness value is exceeded. The sun screen will re-open if the brightness value falls below the threshold. If it is very windy, the sun screen may not be deployed for safety reasons. The corresponding telegram from the brightness sensor, 1 bit if the set brightness value is undershot or overshot, is linked with the UP/DOWN communication object or the communication object Position with the Shutter Actuator. The value 0 of the telegram moves the drive UP, the value 1 moves it DOWN. Safety functions are used with wind, rain and frost. Wind monitoring in particular is required for most systems. For this reason, this function is already integrated into the Shutter Actuators, i.e. there are separate communication objects in existence here. An important basic principle is that the safety functions have a higher priority than classis basic functions. If a safety event occurs, these functions are inhibited, e.g. on-site operation. Furthermore, the drive moves to a freely selectable safety position, e.g. close window with rain or raise shutter with wind.
30 Control functions In the Shutter Actuator, a sequence of priority can be defi ned in addition to the functions wind, rain, frost, forced operation and blocking. In order to achieve safe communication between the Weather Station and the Shutter Actuator, the signals between both devices are monitored. For this purpose it is necessary that a data telegram is cyclically sent from the sensor on the bus. The Shutter Actuator expects this signal regularly. If it does not arrive, the drive is brought to the safety position 3.3.1.1. Wind monitor As the wind is one of the greatest threats for a sun screen, the possible settings are shown using the wind monitor. Fig. 20 The times can be freely set. In practice it is normally suffi cient to set the cycle time of the sensor to 20 to 30 seconds. The monitoring time in the actuator should be programmed to double or triple time duration. This ensures that the function Safety is not implemented immediately in case of loss of one telegram, i.e. in an unfavourable case, strong wind and failure of the sensor, the drive then opens at the very latest after the monitoring time. Furthermore, after the removal of the function Safety on the parameters you can set how the drive should react. It is interesting here to set the parameters to move to saved position, i.e. the state existing beforehand, e.g. the position of the sunscreen, is reassumed. Shutter actuator Weather sensor Sent GA 3/3/1 receives on the communication objectwind GA 3/3/1 0: no wind 1: wind, threshold value exceeded cyclic every 20 s monitoring time 60 s
31 Control functions Settings in Shutter Actuator JA/S x.x parameters – 1 wind monitor is active, 3 are possible – Monitoring period 60 s Fig. 21: Settings in Shutter Actuator JA/S x.x Assignment of wind alarm no. 1 on wind monitor no. 1 – Position on wind alarm: Move UP – Position when retracted: move to saved position Fig. 22: Setting options for every individual wind alarm, here no. 1
32 Control functions Blocking function feature One distinctive feature is provided by the Blocking function which operates without cyclic monitoring. For this purpose, a 1 bit Blocking communication object is available. Before the drive is blocked, it can be moved UP, DOWN or to another position. This blocking is implemented with the assistance of the function Blocking. 3.3.1.2. Weather-dependent sensors At the moment, the following weather dependent sensors are available for the ABB i-bus ® KNX system: Brightness Sensor HS/S 3.1 with 3 brightness threshold values Fig. 23: Brightness Sensor HS/S 3.1 Weather Station WZ/S 1.1 with Weather Sensor WES/A 2.1 WZ/S 1.1 5 L N 6 7 8 U s 1 2 3 4 1 A B 2 Fig. 24: Weather Station WZ/S 1.1 with Weather Sensor WES/A 2.1 Electrically operated curtains and windows are fi tted on an offi ce fl oor. In order to avoid damage, the window may not be open at the same time as the curtains are closed The relevant weather data mentioned above is available with the Weather Station WZ/S 4.1: Brightness from three directions, wind, rain, temperature.
33 Control functions Weather Station WS/S 4.1 with external sensors As in principle it is a 4-fold analogue input with special software, any analogue weather sensors, i.e. 0 … 10 V, 0 … 20 mA, etc. can be used. Fig. 25: Weather Station WS/S 4.1 with external sensors Analogue Input AE/S 4.2 The software of the Analogue Input AE/S 4.2 has fewer functions that the Weather Station WS/S 4.1. The parameters are not adapted to the weather sensors. Fig. 26: Analogue Input AE/S 4.2 WS/S 4.1 A 1 2 B 3 4 5 6 7 8 C D 0 V Un 9 L N 10 11 12 Us
34 Control functions 3.3.2. Temperature dependent control Temperature-dependent controls are very economical, as shutters, roller blinds and awnings always are related to heat and cold protection. Heating up of the building is prevented by the reduction of the suns rays. With closed roller blinds, i.e. typical for a dwelling, the insulation effect of the window is enhanced. This reduces cooling down of the building. The following automatic functions are available: – Automatic sun screening – Automatic heating/cooling – Night cool down 3.3.2.1. Automatic sun screening With the Automatic sun screen there is a link between a Light Sensor and a Shutter Actuator: Fig. 27: Establishment of automatic sun screening The Automatic sun screen function is already included in the Shutter Actuator JA/S x.x. For further information see product manual Shutter Actuators JA/S x.x Automatic sun protection Brightness sensor Preferred sun protection position Push button Sun shutter DOWN and slat CLOSED or move to position No sun blind UP
35 Control functions 3.3.2.2. Automatic heating/cooling The following parameters are linked for the function HEATING/COOLING automatic: – Sun – Blind – Presence of persons – Heating or cooling period Fig. 28 This function is included in the Shutter Actuators. For further information see product manual Shutter Actuators JA/S x.x 3.3.2.3. Night cool down Using the Night cool down automatic function it is possible to implement cooling of rooms by temperature dependent ventilation. It is not useful to always open the window at fi xed times. With the climate in central Europe it may be necessary to suspend this function because of a cool day or night in summer. Brightness sensor Preferred sun protection position Sun shutter down and louvre closing or move to position No sun shutter up Automatic sun protection Push button Motion sensor Thermostat – + The window of a production hall should be opened for cooling early in the morning before work starts in summer.
36 Control functions Implementation of night cool down The internal and external temperatures must be measured for this function: – Internal temperature via thermostat; for several rooms a reference room should be selected or even the mean value of several rooms. – External temperature via Weather Station. Two conditions must also be fulfi lled: – Comparator: The internal temperature is higher than the external temperature. – Threshold: The external temperature is greater than a defi ned fi xed value, e.g. 18 degrees. The two conditions – comparator and threshold – can be detected using a Logic Module LMS 1.1. The principle schematic appears as follows: Fig. 29: Principle schematic There is an enable button and a clock with set time window. In this time period, e.g. between 5 a.m. and 6 a.m. the automatic function Night cool down occurs. With value 1 the window is opened and closed with value 0. Release button Thermostat – + Weather sensor external temperature higher than 18 °C LM/S 1.1 Logic module Shutter actuator internal temperature higher than external temperature Window opening/closing AND logic
37 Control functions Parameter settings and communication objects in the Logic Module LM/S 1.1 Two temperature comparators are required. One sends a logical 1 when the internal tempera- ture is greater than the external temperature; the other one is inverted and sends a 0 when the external temperature is higher than the internal temperature. Fig. 30: Logic Module LM/S 1.1, temperature comparator A Fig. 31: Logic Module LM/S 1.1, temperature comparator B
38 Control functions The threshold is a defi ned value. This is compared to the current external temperature. If it is greater for example than 18 °C, the condition is fulfi lled and logic 1 is sent. This will prevent an extreme cool down during cool nights. Fig. 32: Logic Module LM/S 1.1, function Threshold value For optimisation of this control you can also set the internal temperature to a minimum value, e.g. greater than 22 °C. This will avoid night cool down with a low room temperature. For this purpose, only one further threshold function is required in the LM/S 1.1 and one additional input in the AND gate. If all conditions are fulfi lled, the window can be opened via an AND function with a further Logic Module LM/S 1.1. If at least one condition is not fulfi lled, the window will be closed again. Logic module objects with group addresses: Fig. 33: Group addresses of the communication objects
39 3.3.3. Sun position dependent control A further stage in intelligent sun screening is the sun position-dependent control of blinds. Two function types are available here: – Anti-glare protection – Daylight redirection Anti-glare protection Anti-glare protection protects against direct, glaring sunlight with the admission of the maxi- mum level of diffused light. Fig. 34: Blind setting dependent on sun position In order to implement optimum anti-glare protection, it is important to set the blind height and, if required, the angle of the louvres, so that they comply with the above mentioned characteri- stics. The height and louvre position is automatically adjusted to track the position of the sun. For a full range of functionality, blinds with louvres are necessary. However, this application can also be employed in houses with shutters. If the sun shine, the shutters should close to avoid heating up of a house in summer. The function Anti-glare protection can be employed here. The shutters are only moved when the respective windows are subject to sunshine. The positioning of the shutters is implemented via the shutter height. This is programmed to ensure that the viewing and air slots between the shutters always stay open. Furthermore, the shutters are opened immediately when the window is in the shade again. Control functions
40 Maximum admission of daylight without direct sunlight. Rooms are only shaded when absolutely neces- sary. Accordingly, less artifi cial light is required. Direction of daylight Redirection of daylight protects against direct, glaring sunlight. The natural brightness is opti- mally exploited through selective direction of the sunlight into the room. The objective of this application is controlled infl ow of sunlight to the room. The sunlight is directed onto the ceiling by tracking of the louvre angle, where it brightens the room through indirect but natural lighting. Fig. 35: Optimum daylight utilization through louvre angle tracking Maximum admission of natural light into the room without direct glare. Additional room heating during the summer months. The inner surfaces of the louvres must be refl ective for the best results. Control functions
41 Function of a sun position-dependent blind control 1 0 Automatic control activated Automatic control deactivated 1 = sunand 8 bit valve 0 = no sun Move to 8 bit position Position at sun = 0 Direct positioning via UP/DOWN or move in position Brightness sensor Shutter control module o o Fig. 36: Function chart of sun-dependent blind control The brightness sensor detects whether the sun shines onto the facade and thus into the rooms. Ideally, each facade should feature a sensor. In Europe, for example, three sensors for South, West and East. A corresponding brightness threshold is set in the sensors. If this threshold is exceeded, the sun position-dependent control tracks the position of the sun. The quality of the light sensor with the accuracy of the brightness threshold is decisive to ensure a good function. The use of the Weather Sensor WES/A 2.1 with the Weather Unit WZ/S 1.1 is not recommended! The Weather Station WES/A 4.1 offers all options together with high-quality external sensors. The Shutter Control Unit JSB/S 1.1 as the central intelligent module assumes the sun protection control and controls the position via an 8 bit telegram. It is necessary to set some parameters for correct JSB/S function incl.: – Alignment of the building with regard to its geographical orientation – Date and time – Building location (longitude and latitude) – Geometry of the window and sun protection A local push button should be available to switch off the automatic control. For example, in winter, the occupants may desire the sun to shine directly into the building for the purpose of heating the building or personal well-being. If other buildings or objects, e.g. trees, are located in front of a facade, they will be a source of shadow. They can be included in the calculation by entering the corresponding data (distance and size). The course of the shadow cast is calculated as well as the exact time period for which a window is sub- ject to the shadow of the shadow-caster. Control functions
42 Fig. 37: Infl uence of a shadow caster The functions anti-glare protection and daylight redirection with the assistance of Shutter Control Unit JSB/S 1.1 only function with the Shutter Actuators JA/S from ABB. Only these devices feature the necessary parameters and communicatuion objects as explained in the following. Detailed information regarding the planning and programming can be found in the product manual of the Shutter Control Unit JSB/S 1.1 Communication between Shutter Control Unit JSB/S 1.1 and ABB i-bus ® KNX blind actuators The JSB/S 1.1 controls the blind actuators via three communication objects: – Sun (yes/no, 1 bit) – Position sun screen (blind height, 1 byte) – Position louvres (louvre angle, 1 byte) Using the communication object Sun (value 1), the outputs of the blind actuator are informed that the sun is shining on the respective window, or alternatively that the programmed bright- ness value is exceeded. The blind is moved into a position compliant with the programming (blind height and/or louvre angle). If the communication object Sun has the value 0 (brightness threshold undershoot), the drive will move in accordance with the programming in the blind actuator, e.g. UP or to any other position. Control functions
43 In the following, you can see the required implementation parameters: Fig. 38: Parameter function Automatic shutter actuator After automatic control is enabled in the parameter windows X General (X = A…X), the actions for sun position-controlled blind control are set in the parameter window Auto 1. It is important to select the option Receive position via 8 bit values in the parameter Position if sun = 1. The parameter Position if sun = 0 is generally parameterised with UP, but other positions can be selected. In the following fi gure, the communication objects of the blind actuator and blind actuator mo- dules are shown, as well as the assignment of the group addresses of the three communication objects already mentioned: Control functions
44 Communication object No. 4 Sensor no. 1 represents the connection to the brightness sensor. Up to 4 communication objects for sensors can be activated. Fig. 39: Assignment of the group addresses shutter actuator and shutter modules After parameterization of the basic functions in the JSB/S 1.1 (see above) and the settings stated in the blind actuator, the function of the sun position-dependent control is guaranteed in principle. Without shadow casters, a detailed examination of the facade or windows is not necessary, as all facade surfaces are subject to the same degree of sunshine. Afterwards, the function is optimised further, e.g. the brightness threshold or blind height during sunshine are adjusted. The setup is more comprehensive, should the facade be subject to shadow-casters. The shadow caster data such as the size and distance from the facade must be determined. Detailed information such as the window size and distances to the window are required. The corresponding set-up times should be considered. A complete planning checklist intended especially for sun position-dependent blind control can be found in the product manual of the JSB/S 1.1. Control functions
45 Notes
46 Notes
47 Roller Blind/Shutter Control Building: Level: Room: Smallest common controlled unit no.: Function: Intended shutter/blinds: ❏ Internal shutter vertical ❏ Number ❏ Drive ❏ 230 V AC ❏ 24 V DC ❏ 12 V DC ❏ SMI ❏ Other ❏ Current consumption ❏ Reversal time ❏ Travel time ❏ Mechanical end limit switches ❏ Switch off via increased current ❏ No switch off via end switch or increased current ❏ Installation location ❏ Internal shading ❏ Number ❏ Drive ❏ 230 V AC ❏ 24 V DC ❏ 12 V DC ❏ SMI ❏ Other ❏ Current consumption ❏ Reversal time ❏ Travel time ❏ Mechanical end limit switches ❏ Switch off via increased current ❏ No switch off via end switch or increased current ❏ Installation location Checklist
48 ❏ External shutter ❏ Number ❏ Drive ❏ 230 V AC ❏ 24 V DC ❏ 12 V DC ❏ SMI ❏ Other ❏ Current consumption ❏ Reversal time ❏ Travel time ❏ Mechanical end limit switches ❏ Switch off via increased current ❏ No switch off via end switch or increased current ❏ Installation location Manual on-site operation ❏ Conventional push button/switch with fl ush mounted interface ❏ 1 push button (short = lamella, long = moving) ❏ 1 push button (short = Move, long = Lamella) ❏ 1 push button, move only ❏ 1 switch operation, move only ❏ 2 push button, standard ❏ 2 switch operation, move only (roller blinds) ❏ 2 push button operation, move only (roller blinds) ❏ 2 push buttons (only Lamella) ❏ Push buttons: Additional functions: ❏ Other free rocker used for ❏ Status feedback via LED ❏ Orientation light ❏ Bus push button Make: Design: ❏ Other free rocker used for ❏ Additional functions: ❏ Status feedback via LED ❏ Orientation light ❏ Number of assigned push buttons ❏ Installation locations Checklist
49 Superior manual operation ❏ Central operation ❏ Central UP ❏ Central DOWN ❏ Superior group circuit ❏ Number of groups ❏ Function ❏ Integration into manually controlled scenes ❏ Number of scenes ❏ Behaviour with scene call Automatic control on-site ❏ Controlled with other events on-site ❏ ❏ Superior automatic control ❏ Automatic shading – with sun ❏ No reaction ❏ DOWN ❏ UP ❏ STOP ❏ Predefi ned position ❏ Position setting via superior control ❏ Automatic shading – no sun ❏ No reaction ❏ DOWN ❏ UP ❏ STOP ❏ Predefi ned position ❏ HEATING/COOLING automatic ❏ HEATING + sun ❏ no reaction ❏ DOWN ❏ UP ❏ STOP ❏ Predefi ned position ❏ HEATING + no sun ❏ no reaction ❏ DOWN ❏ UP ❏ STOP ❏ Predefi ned position Checklist
50 ❏ COOLING + sun ❏ No reaction ❏ DOWN ❏ UP ❏ STOP ❏ Predefi ned position ❏ COOLING + no sun ❏ No reaction ❏ DOWN ❏ UP ❏ STOP ❏ Predefi ned position ❏ Timer ❏ Weekly timer program ❏ Yearly timer program ❏ Number of daily sequences ❏ Number of special days ❏ Twilight switch ❏ Move UP at l x ❏ Move DOWN at l x ❏ Integration into automatically controlled scenes ❏ Number of scenes ❏ Behaviour with scene call ❏ Controlled with other superior events ❏ ❏ Checklist
51 Safety functions ❏ Behaviour on wind alarm ❏ Deactivated (does not react to wind alarm) ❏ Activated – no reaction (movement is ended and then blocked) ❏ Activated – UP ❏ Activated – DOWN ❏ Activated – STOP ❏ Behaviour on frost alarm ❏ Deactivated (does not react to frost alarm) ❏ Activated – no reaction (movement is ended and then blocked) ❏ Activated – UP ❏ Activated – DOWN ❏ Activated – STOP ❏ Behaviour on rain alarm ❏ Deactivated (does not react to rain alarm) ❏ Activated – no reaction (movement is ended and then blocked) ❏ Activated – UP ❏ Activated – DOWN ❏ Activated – STOP ❏ Priorities of weather alarms Wind alarm Rain alarm Frost alarm ❏ Behaviour when blocked (e.g. for cleaning) ❏ Deactivated (does not react to block) ❏ Activated – no reaction (movement is ended and then blocked) ❏ Activated – UP ❏ Activated – DOWN ❏ Activated – STOP ❏ Activated – move to position (blind-shutter height/louvre setting) ❏ Enable forced operation ❏ Priorities of the functions Safety Weather alarm Block Forced operation Checklist
52 Operation/display at a remote location ❏ Remote controlled ❏ Via telephone ❏ Via LAN ❏ Via Internet ❏ Status message ❏ On visualisation system ❏ Query via telephone ❏ Query via LAN ❏ Query via Internet Special functions ❏ Integration in occupancy simulation ❏ Inhibit on-site operation at certain times ❏ Times: ❏ Behaviour on inhibit removal ❏ UP ❏ DOWN ❏ State as beforehand ❏ As last “attempted” manual on-site operation ❏ Inhibit on-site operation for certain events/states ❏ Events: ❏ Allow only UP movement at certain times ❏ Allow only DOWN movement at certain times ❏ Switch from certain points with higher priority (forced operation) Behaviour on priority removal ❏ UP ❏ DOWN ❏ State as beforehand ❏ As last “attempted” manual on-site operation ❏ Partition function ❏ As an open partition common control with Checklist
Note: We reserve the right to make technical changes or modify the contents of this document without prior notice. With regard to purchase orders, the agreed particulars shall prevail. ABB AG does not accept any responsibility whatsoever for potential errors or possible lack of information in this document. We reserve all rights in this document and in the subject matter and illustrations contained therein. Any reproduction, disclosure to third parties or utilization of its contents - in whole or in parts - is forbidden without prior written consent of ABB AG. Copyright© 2010 ABB All rights reserved www.abb.com/knx Contact Or der Number 2CDC 500 057 M0202 (04/10)