Shopping Cart
Distributor Selection
Select the distributor you would like to use for your shopping cart.
Distributor
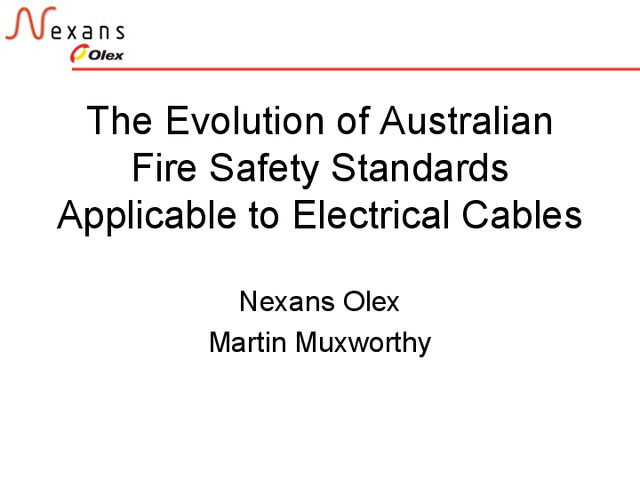
Webinar Presentation on Safely protecting the electric cable and the environment through correct MCB and cable selection
According to statistical data many building fires have been attributed to electrical faults. Often the source of the fire can be traced to an incorrectly designed electrical system allowing cables to operate at temperatures beyond their operating limits, resulting in failure and eventual fire.
The Evolution of Australian Fire Safety Standards Applicable to Electrical Cables Nexans Olex Martin Muxworthy
The Evolution of Australian Fire Safety Standards Applicable to Electrical Cables Nexans Olex Martin Muxworthy
The Evolution of Australian Fire Safety Standards Applicable to Electrical Cables • Agenda – Overview of essential characteristics of Fire Rated cables – Applicable standards to confirm these characteristics – What are the differences between the Australian and other International standards for fire testing of cables – How fire rated cables are constructed – How the fire testing standards for cables are aligned with the building industry
The Evolution of Australian Fire Safety Standards Applicable to Electrical Cables • Agenda – Overview of essential characteristics of Fire Rated cables – Applicable standards to confirm these characteristics – What are the differences between the Australian and other International standards for fire testing of cables – How fire rated cables are constructed – How the fire testing standards for cables are aligned with the building industry
The Evolution of Australian Fire Safety Standards Applicable to Electrical Cables • Fundamental characteristics of Fire Rated cables – Flame retardant – do not propagate fire – Low smoke – assists in evacuation of buildings during fire – Zero halogen – does not create toxic fumes and corrosive by-products during fire – Maintains circuits integrity – keeps electrical equipment going during fire
The Evolution of Australian Fire Safety Standards Applicable to Electrical Cables • Fundamental characteristics of Fire Rated cables – Flame retardant – do not propagate fire – Low smoke – assists in evacuation of buildings during fire – Zero halogen – does not create toxic fumes and corrosive by-products during fire – Maintains circuits integrity – keeps electrical equipment going during fire
The Evolution of Australian Fire Safety Standards Applicable to Electrical Cables • Flame retardant cables – Does not propagate fire (self extinguishing)– Retards the spread of fire – They are used in buildings, plants, enclosed infrastructure and ships • Avoid spreading fire from one area to another• Avoid adding fuel to a fire – Incorporate flame retardant materials in the cable sheathing
The Evolution of Australian Fire Safety Standards Applicable to Electrical Cables • Flame retardant cables – Does not propagate fire (self extinguishing)– Retards the spread of fire – They are used in buildings, plants, enclosed infrastructure and ships • Avoid spreading fire from one area to another• Avoid adding fuel to a fire – Incorporate flame retardant materials in the cable sheathing
The Evolution of Australian Fire Safety Standards Applicable to Electrical Cables • Flame retardant cables – Material tests • Oxygen index AS/NZS 2122.2 (% Oxygen in air that supports combustion of material) • Oxygen index of 30+ (Air contains 21% oxygen) – Cable tests • Single cable vertical propagation test – 600 mm cable length, 1200 mm high chamber– Time duration varies with cable size– AS/NZS 5000 Pass criteria » Charring 50mm from top support and» Falling particles not allowed to ignite paper underlay • AS/NZS 1660.5.6 (2005)• Originated from AS 1660.4 (1974)• Current version adopts the content of IEC 60332-1• IEC 60332-1 first published as IEC 60332 in 1970
The Evolution of Australian Fire Safety Standards Applicable to Electrical Cables • Flame retardant cables – Material tests • Oxygen index AS/NZS 2122.2 (% Oxygen in air that supports combustion of material) • Oxygen index of 30+ (Air contains 21% oxygen) – Cable tests • Single cable vertical propagation test – 600 mm cable length, 1200 mm high chamber– Time duration varies with cable size– AS/NZS 5000 Pass criteria » Charring 50mm from top support and» Falling particles not allowed to ignite paper underlay • AS/NZS 1660.5.6 (2005)• Originated from AS 1660.4 (1974)• Current version adopts the content of IEC 60332-1• IEC 60332-1 first published as IEC 60332 in 1970
The Evolution of Australian Fire Safety Standards Applicable to Electrical Cables • Flame retardant cables – Cable tests • Multiple (bunched) cable vertical propagation test – 3.5 m lengths of cable– Defined volume of combustible material » Could be a single large cable; or» Could be many, ie 10, 15 or 20 small cables» Pass if flames do not propagate further than 2.5 m from burner at bottom • AS/NZS 1660.5.1 (2005)• Originated from SAA Int 880011 (1988)• Current version adopts the content of IEC 60332-3 • IEC 60332-3 first published as IEC 60332-3 in 1982
The Evolution of Australian Fire Safety Standards Applicable to Electrical Cables • Flame retardant cables – Cable tests • Multiple (bunched) cable vertical propagation test – 3.5 m lengths of cable– Defined volume of combustible material » Could be a single large cable; or» Could be many, ie 10, 15 or 20 small cables» Pass if flames do not propagate further than 2.5 m from burner at bottom • AS/NZS 1660.5.1 (2005)• Originated from SAA Int 880011 (1988)• Current version adopts the content of IEC 60332-3 • IEC 60332-3 first published as IEC 60332-3 in 1982
The Evolution of Australian Fire Safety Standards Applicable to Electrical Cables • Low smoke zero halogen cables – Cables that are made from materials that DO NOT contain halogens – Cables that emit low level or no smoke, no toxic fumes and no corrosive gases – Used in confined areas with large amount of cables within close proximity to human traffic and/or presence of sensitive electronic equipment • Avoid low visibility caused by smoke• Avoid harmful effects on humans due to inhalation of toxic fumes • Avoid corrosion of sensitive electronics
The Evolution of Australian Fire Safety Standards Applicable to Electrical Cables • Low smoke zero halogen cables – Cables that are made from materials that DO NOT contain halogens – Cables that emit low level or no smoke, no toxic fumes and no corrosive gases – Used in confined areas with large amount of cables within close proximity to human traffic and/or presence of sensitive electronic equipment • Avoid low visibility caused by smoke• Avoid harmful effects on humans due to inhalation of toxic fumes • Avoid corrosion of sensitive electronics
The Evolution of Australian Fire Safety Standards Applicable to Electrical Cables • Low smoke cables – Smoke Density – AS/NZS 1660.5.2 (2006)– 3 m cube smoke chamber • Burning a set volume of cable material• Checking the amount of light transmitted through the chamber • AS/NZS 4507 pass if 50-70% light transmitted – Originated from AS 1660.5.2 (1992)– Current version adopts the content of IEC 61034 – IEC 61034 • Part 1 (test apparatus) first published in 1990• Part 2 (test procedure and requirements) first published as TS 61034-2 in 1991
The Evolution of Australian Fire Safety Standards Applicable to Electrical Cables • Low smoke cables – Smoke Density – AS/NZS 1660.5.2 (2006)– 3 m cube smoke chamber • Burning a set volume of cable material• Checking the amount of light transmitted through the chamber • AS/NZS 4507 pass if 50-70% light transmitted – Originated from AS 1660.5.2 (1992)– Current version adopts the content of IEC 61034 – IEC 61034 • Part 1 (test apparatus) first published in 1990• Part 2 (test procedure and requirements) first published as TS 61034-2 in 1991
The Evolution of Australian Fire Safety Standards Applicable to Electrical Cables • Zero halogen cables – Acidity – AS/NZS 1660.5.3 (1998)– Material test • Burning a small sample of cable material in tube furnace• Determines the amount of halogen acid gas evolved during combustion • Volume of hydrochloric acid determined – LSZH cables return zero halogen acid – Originated from AS 1660.5.3 (1988)– Current version aligns with content of IEC 754-1 (1994)– IEC 60754-1 • Latest version 2011• First published in 1982
The Evolution of Australian Fire Safety Standards Applicable to Electrical Cables • Zero halogen cables – Acidity – AS/NZS 1660.5.3 (1998)– Material test • Burning a small sample of cable material in tube furnace• Determines the amount of halogen acid gas evolved during combustion • Volume of hydrochloric acid determined – LSZH cables return zero halogen acid – Originated from AS 1660.5.3 (1988)– Current version aligns with content of IEC 754-1 (1994)– IEC 60754-1 • Latest version 2011• First published in 1982
The Evolution of Australian Fire Safety Standards Applicable to Electrical Cables • Zero halogen cables – Corrosivity – AS/NZS 1660.5.4 (1998)– Material test • Same test apparatus as AS/NZS 1660.5.3 for acidity• Burning a small sample of cable material in tube furnace• Determines the pH of gases evolved during combustion• Conductivity is also measured – AS/NZS 4507 pass pH 3.5, and conductivity 10uS/mm – Originated from SAA Int 88003 (1988)– Current version aligns with content of IEC 754-2 (1991)– IEC 60754-2 • Latest version 2011• First published in 1991
The Evolution of Australian Fire Safety Standards Applicable to Electrical Cables • Zero halogen cables – Corrosivity – AS/NZS 1660.5.4 (1998)– Material test • Same test apparatus as AS/NZS 1660.5.3 for acidity• Burning a small sample of cable material in tube furnace• Determines the pH of gases evolved during combustion• Conductivity is also measured – AS/NZS 4507 pass pH 3.5, and conductivity 10uS/mm – Originated from SAA Int 88003 (1988)– Current version aligns with content of IEC 754-2 (1991)– IEC 60754-2 • Latest version 2011• First published in 1991
The Evolution of Australian Fire Safety Standards Applicable to Electrical Cables • Circuit Integrity – Keeps electrical equipment going during fire– Terms - Fire resistant, Fire Rated– Used in buildings, plants, enclosed infrastructure, ships and sites where the cable is expected to continue to function for essential services/mission critical applications whilst under fire. – Fire Safety in Buildings – Fire Alarm and Security cabling– Emergency Exit signs and facilities– Power and control for Fire Fighting equipment eg Water Pumps • Standards for Circuit Integrity – Ribbon burner (IEC 60331, AS/NZS 1660.5.5, BS 6387)– Furnace (AS/NZS 3013)
The Evolution of Australian Fire Safety Standards Applicable to Electrical Cables • Circuit Integrity – Keeps electrical equipment going during fire– Terms - Fire resistant, Fire Rated– Used in buildings, plants, enclosed infrastructure, ships and sites where the cable is expected to continue to function for essential services/mission critical applications whilst under fire. – Fire Safety in Buildings – Fire Alarm and Security cabling– Emergency Exit signs and facilities– Power and control for Fire Fighting equipment eg Water Pumps • Standards for Circuit Integrity – Ribbon burner (IEC 60331, AS/NZS 1660.5.5, BS 6387)– Furnace (AS/NZS 3013)
The Evolution of Australian Fire Safety Standards Applicable to Electrical Cables • Circuit Integrity (cont’d) – It is implied that a Fire Resistant cable should be Flame retardant and Low Smoke Zero Halogen as well but it is not necessarily the case” • Ribbon burner standards – AS/NZS 1660.5.5 (2005) now adopts the content of IEC 60331 – Originated from AS/NZS 1660.5.5 (1998)– IEC 60331 • First published in 1970• Latest version 2009• Has gone through a number of revisions• Now comprises sub parts 1, 2, 3, 11, 21, 23, 25, 31 – Depending on temperature, cable type, mechanical shock, water
The Evolution of Australian Fire Safety Standards Applicable to Electrical Cables • Circuit Integrity (cont’d) – It is implied that a Fire Resistant cable should be Flame retardant and Low Smoke Zero Halogen as well but it is not necessarily the case” • Ribbon burner standards – AS/NZS 1660.5.5 (2005) now adopts the content of IEC 60331 – Originated from AS/NZS 1660.5.5 (1998)– IEC 60331 • First published in 1970• Latest version 2009• Has gone through a number of revisions• Now comprises sub parts 1, 2, 3, 11, 21, 23, 25, 31 – Depending on temperature, cable type, mechanical shock, water
The Evolution of Australian Fire Safety Standards Applicable to Electrical Cables • Circuit Integrity (cont’d) – Ribbon Burner Standards • AS/NZS 1660.5.5/IEC 60331 – Fire alone (≥750 o C) – Fire and mechanical shock (≥830 o C) – Water (optional)
The Evolution of Australian Fire Safety Standards Applicable to Electrical Cables • Circuit Integrity (cont’d) – Ribbon Burner Standards • AS/NZS 1660.5.5/IEC 60331 – Fire alone (≥750 o C) – Fire and mechanical shock (≥830 o C) – Water (optional)
The Evolution of Australian Fire Safety Standards Applicable to Electrical Cables • Circuit Integrity (cont’d) – Ribbon Burner Standards• BS 6387 – Similar test apparatus to IEC 60331 (Test for shock, cable is mounted on fire rated board) – First published 1983– Latest version 2013– Cat. A = 650 o C, Cat. B = 750 o C & Cat. C = 950 o C – Cat. W = Fire 650 o C with sprinkler water – Cat. X = 650 o C under shock, Cat. Y = 750 o C under shock, Cat. Z = 950 o C under shock – Eg BS 6387 Cat C, W, Z
The Evolution of Australian Fire Safety Standards Applicable to Electrical Cables • Circuit Integrity (cont’d) – Ribbon Burner Standards• BS 6387 – Similar test apparatus to IEC 60331 (Test for shock, cable is mounted on fire rated board) – First published 1983– Latest version 2013– Cat. A = 650 o C, Cat. B = 750 o C & Cat. C = 950 o C – Cat. W = Fire 650 o C with sprinkler water – Cat. X = 650 o C under shock, Cat. Y = 750 o C under shock, Cat. Z = 950 o C under shock – Eg BS 6387 Cat C, W, Z
The Evolution of Australian Fire Safety Standards Applicable to Electrical Cables • Circuit Integrity (cont’d) – Furnace Standards• AS/NZS 3013 – Current version 2005– First published in 1990 • Differences to ribbon burner standards – Test done in furnace (different environment to ribbon burner tests)– Test method applicable to all wiring system elements • Cables, busways, supports (trays) and fixings (saddles, ties) – Cable tested on cable trays • Previous version cable clipped to roof of fire chamber – Additional water spray test to simulate fire extinguishing methods used in practice – Defined time/temperature curve in accordance with AS 1530.4
The Evolution of Australian Fire Safety Standards Applicable to Electrical Cables • Circuit Integrity (cont’d) – Furnace Standards• AS/NZS 3013 – Current version 2005– First published in 1990 • Differences to ribbon burner standards – Test done in furnace (different environment to ribbon burner tests)– Test method applicable to all wiring system elements • Cables, busways, supports (trays) and fixings (saddles, ties) – Cable tested on cable trays • Previous version cable clipped to roof of fire chamber – Additional water spray test to simulate fire extinguishing methods used in practice – Defined time/temperature curve in accordance with AS 1530.4
The Evolution of Australian Fire Safety Standards Applicable to Electrical Cables • Circuit Integrity (cont’d) – Furnace Standards (AS/NZS 3013) – WS classification system, eg WS52W • WS = “Wiring System”• First numeral indicates time for which cables or busways are able to maintain circuit integrity, eg – 1 = 15 minutes– 2 = 30 minutes– 3 = 60 minutes– 4 = 90 minutes– 5 = 120 minutes (2 hours commonly requested) • Second numeral represents degree of mechanical impact and cutting force that wiring system element can withstand without failure – 1 = Light (2.5 Joule Impact & 0.3 kN Cutting)– 2 = Moderate (15 Joule Impact & 1.0 kN Cutting) (2 is common for cables)– 3 = Heavy (50 Joule Impact & 5.0 kN Cutting)– 4 = Very Heavy (500 Joule Impact & 5.0 kN Cutting)– 5 = Extremely Heavy (5000 Joule Impact & 5.0 kN Cutting) • Supplementary letter “W” represents additional water spray test
The Evolution of Australian Fire Safety Standards Applicable to Electrical Cables • Circuit Integrity (cont’d) – Furnace Standards (AS/NZS 3013) – WS classification system, eg WS52W • WS = “Wiring System”• First numeral indicates time for which cables or busways are able to maintain circuit integrity, eg – 1 = 15 minutes– 2 = 30 minutes– 3 = 60 minutes– 4 = 90 minutes– 5 = 120 minutes (2 hours commonly requested) • Second numeral represents degree of mechanical impact and cutting force that wiring system element can withstand without failure – 1 = Light (2.5 Joule Impact & 0.3 kN Cutting)– 2 = Moderate (15 Joule Impact & 1.0 kN Cutting) (2 is common for cables)– 3 = Heavy (50 Joule Impact & 5.0 kN Cutting)– 4 = Very Heavy (500 Joule Impact & 5.0 kN Cutting)– 5 = Extremely Heavy (5000 Joule Impact & 5.0 kN Cutting) • Supplementary letter “W” represents additional water spray test
The Evolution of Australian Fire Safety Standards Applicable to Electrical Cables • Circuit Integrity (cont’d) – Furnace Standards• AS/NZS 3013 – Circuit Integrity During Fire
The Evolution of Australian Fire Safety Standards Applicable to Electrical Cables • Circuit Integrity (cont’d) – Furnace Standards• AS/NZS 3013 – Circuit Integrity During Fire
The Evolution of Australian Fire Safety Standards Applicable to Electrical Cables • Circuit Integrity (cont’d) – Furnace Standards• AS/NZS 3013/AS 1530.4 Time/Temperature Curve
The Evolution of Australian Fire Safety Standards Applicable to Electrical Cables • Circuit Integrity (cont’d) – Furnace Standards• AS/NZS 3013/AS 1530.4 Time/Temperature Curve
The Evolution of Australian Fire Safety Standards Applicable to Electrical Cables • Circuit Integrity (cont’d) – Furnace Standards • AS/NZS 3013 – Mechanical Rating Impact Test Setup Cutting Test Setup
The Evolution of Australian Fire Safety Standards Applicable to Electrical Cables • Circuit Integrity (cont’d) – Furnace Standards • AS/NZS 3013 – Mechanical Rating Impact Test Setup Cutting Test Setup
The Evolution of Australian Fire Safety Standards Applicable to Electrical Cables • Fire Rated Cables – Construction – MIMS (Mineral Insulated Metal Sheathed) • Invented in 1896• Magnesium Oxide insulation• Copper conductor/Copper sheath – Mica/Glass Tape • Developed 1970s• XLPE, Rubber insulation• HFS, Rubber sheath – Ceramifiable® Materials • Developed 2004 By Olex/CSIRO• Special insulation material turns hard (ceramic) during fire • HFS sheath Alsecure® Plus Alsecure® Premium
The Evolution of Australian Fire Safety Standards Applicable to Electrical Cables • Fire Rated Cables – Construction – MIMS (Mineral Insulated Metal Sheathed) • Invented in 1896• Magnesium Oxide insulation• Copper conductor/Copper sheath – Mica/Glass Tape • Developed 1970s• XLPE, Rubber insulation• HFS, Rubber sheath – Ceramifiable® Materials • Developed 2004 By Olex/CSIRO• Special insulation material turns hard (ceramic) during fire • HFS sheath Alsecure® Plus Alsecure® Premium
The Evolution of Australian Fire Safety Standards Applicable to Electrical Cables • Linking Cable Fire Safety and Building Standards – AS 1530.4 – Fire resistance of building materials • Walls, floors, roofs, columns, beams, door assemblies, ducts, critical services, etc. • Referenced in ABCB National Construction Code• Tests FRL of material (Fire Resistance Level) xx/yy/zz (time in minutes to failure) – xx Structural adequacy (eg load bearing elements)– yy Integrity (maintains barrier to prevent flames or hot gases passing through) – zz Insulation (minimises temperature rise of the exposed face of building element) • Some examples – Emergency lift shafts 120/120/120– Main switchboards supplying emergency equipment 120/120/120
The Evolution of Australian Fire Safety Standards Applicable to Electrical Cables • Linking Cable Fire Safety and Building Standards – AS 1530.4 – Fire resistance of building materials • Walls, floors, roofs, columns, beams, door assemblies, ducts, critical services, etc. • Referenced in ABCB National Construction Code• Tests FRL of material (Fire Resistance Level) xx/yy/zz (time in minutes to failure) – xx Structural adequacy (eg load bearing elements)– yy Integrity (maintains barrier to prevent flames or hot gases passing through) – zz Insulation (minimises temperature rise of the exposed face of building element) • Some examples – Emergency lift shafts 120/120/120– Main switchboards supplying emergency equipment 120/120/120
© ABB STOTZ-KONTAKT GmbH 2CDC 002 154 N0201 | Slide 1 Safely protecting the electric cable and the environment through correct MCB and cable selection Ian Richardson, ABB Australia, July 2016
© ABB STOTZ-KONTAKT GmbH 2CDC 002 154 N0201 | Slide 1 Safely protecting the electric cable and the environment through correct MCB and cable selection Ian Richardson, ABB Australia, July 2016
© ABB STOTZ-KONTAKT GmbH 2CDC 002 154 N0201 | Slide 2 Correct MCB selection to protect cables Basics of line protection / operation Overcurrent protection Overload protection Protection of cables and wires aswell as system parts againstexcessive heating duringoperating overload in a fault-freecircuit by a delayed switch-off Short-circuit protection Protection of cables and wires as well as system parts against the effects of a dead short-circuit between conductors with a different potential by current- limiting switch-off
© ABB STOTZ-KONTAKT GmbH 2CDC 002 154 N0201 | Slide 2 Correct MCB selection to protect cables Basics of line protection / operation Overcurrent protection Overload protection Protection of cables and wires aswell as system parts againstexcessive heating duringoperating overload in a fault-freecircuit by a delayed switch-off Short-circuit protection Protection of cables and wires as well as system parts against the effects of a dead short-circuit between conductors with a different potential by current- limiting switch-off
© ABB STOTZ-KONTAKT GmbH 2CDC 002 154 N0201 | Slide 3 Correct MCB selection to protect cables Basics of line protection / operation Cables and wires must be protected against heating up impermissibly Excessive thermal loading leads to premature aging of the insulation material As a consequence, leakage current and arcing can occur, and as a further consequence also short-circuits It may also be necessary to protect other electric equipment against overcurrents
© ABB STOTZ-KONTAKT GmbH 2CDC 002 154 N0201 | Slide 3 Correct MCB selection to protect cables Basics of line protection / operation Cables and wires must be protected against heating up impermissibly Excessive thermal loading leads to premature aging of the insulation material As a consequence, leakage current and arcing can occur, and as a further consequence also short-circuits It may also be necessary to protect other electric equipment against overcurrents
© ABB STOTZ-KONTAKT GmbH 2CDC 002 154 N0201 | Slide 4 Correct MCB selection to protect cables Protection against overload current Selection of the rated current (previously: nominal current) of the overcurrent protection device according to AS/NZS3000 clause 2.5.3 I b ≤ I n ≤ I z (1) I 2 ≤ 1.45 x I z (2) I n = rated current of the overcurrent protection device I b = operating current of the circuit (e.g. maximum demand) I z = permissible current carrying capacity of cable / wire (AS/NZS3008) I 2 = thermal tripping current of the overcurrent protection device
© ABB STOTZ-KONTAKT GmbH 2CDC 002 154 N0201 | Slide 4 Correct MCB selection to protect cables Protection against overload current Selection of the rated current (previously: nominal current) of the overcurrent protection device according to AS/NZS3000 clause 2.5.3 I b ≤ I n ≤ I z (1) I 2 ≤ 1.45 x I z (2) I n = rated current of the overcurrent protection device I b = operating current of the circuit (e.g. maximum demand) I z = permissible current carrying capacity of cable / wire (AS/NZS3008) I 2 = thermal tripping current of the overcurrent protection device
© ABB STOTZ-KONTAKT GmbH 2CDC 002 154 N0201 | Slide 5 Correct MCB selection to protect cables Protection against overload current Current I Operating conditionsof the cable Tripping characteristicsof the overcurrentprotective device 0 Additional reserve if I 2 1.45 x I n . I 2 I 2 value depends upon tripping curve of the MCB
© ABB STOTZ-KONTAKT GmbH 2CDC 002 154 N0201 | Slide 5 Correct MCB selection to protect cables Protection against overload current Current I Operating conditionsof the cable Tripping characteristicsof the overcurrentprotective device 0 Additional reserve if I 2 1.45 x I n . I 2 I 2 value depends upon tripping curve of the MCB
© ABB STOTZ-KONTAKT GmbH 2CDC 002 154 N0201 | Slide 6 Correct MCB selection to protect cables Typical tripping characteristics of MCB’s B, C, D according to IEC 60898 K, Z according to IEC 60947
© ABB STOTZ-KONTAKT GmbH 2CDC 002 154 N0201 | Slide 6 Correct MCB selection to protect cables Typical tripping characteristics of MCB’s B, C, D according to IEC 60898 K, Z according to IEC 60947
Conductor as heat loss generator Insulation Core R I © ABB STOTZ-KONTAKT GmbH 2CDC 002 154 N0201 | Slide 7 Correct MCB selection to protect cables Heating of conductors Electrical resistance of conductor: l • ρ R = —— A ρ = specific Cu resistance, temperature-dependent Heat power: P = I² • R Heat quantity in the time t: Q = I² • R • t
Conductor as heat loss generator Insulation Core R I © ABB STOTZ-KONTAKT GmbH 2CDC 002 154 N0201 | Slide 7 Correct MCB selection to protect cables Heating of conductors Electrical resistance of conductor: l • ρ R = —— A ρ = specific Cu resistance, temperature-dependent Heat power: P = I² • R Heat quantity in the time t: Q = I² • R • t
© ABB STOTZ-KONTAKT GmbH 2CDC 002 154 N0201 | Slide 8 Correct MCB selection to protect cables H eating of conductors T L Illustration of heat flow Thermal resistance W T U Θ 200°C 180°C 20°C 30 A 100°C 80°C 20°C 20 A 40°C 20°C 20°C 10 A T L T L – T U T U I Example: Heat flow = Higher current - higher power loss - higher heat loss - higher temperature difference - T L increases (proport. to I²) T L – T U W
© ABB STOTZ-KONTAKT GmbH 2CDC 002 154 N0201 | Slide 8 Correct MCB selection to protect cables H eating of conductors T L Illustration of heat flow Thermal resistance W T U Θ 200°C 180°C 20°C 30 A 100°C 80°C 20°C 20 A 40°C 20°C 20°C 10 A T L T L – T U T U I Example: Heat flow = Higher current - higher power loss - higher heat loss - higher temperature difference - T L increases (proport. to I²) T L – T U W
Current carrying capacity I Z of a conductor … ... is determined by conductor resistance per length unit Conductor material Conductor cross section Maximum thermal withstand capacity of the conductor insulation (material) Ambient temperature Heat dissipation to the environment (way of installation) Mutual influencing of several conductors (number of loaded cores, conductor accumulation) … is a characteristic when selecting overcurrent protective devices © ABB STOTZ-KONTAKT GmbH 2CDC 002 154 N0201 | Slide 9 Correct MCB selection to protect cables Current carrying capacity
Current carrying capacity I Z of a conductor … ... is determined by conductor resistance per length unit Conductor material Conductor cross section Maximum thermal withstand capacity of the conductor insulation (material) Ambient temperature Heat dissipation to the environment (way of installation) Mutual influencing of several conductors (number of loaded cores, conductor accumulation) … is a characteristic when selecting overcurrent protective devices © ABB STOTZ-KONTAKT GmbH 2CDC 002 154 N0201 | Slide 9 Correct MCB selection to protect cables Current carrying capacity
© ABB STOTZ-KONTAKT GmbH 2CDC 002 154 N0201 | Slide 10 Correct MCB selection to protect cables Thermal aging of conductors Typical values for the thermal loading capacity are: 2.5 25 Years Material Overload Short- circuit EPR 60°C 250°C PVC 70°C 160°C PVC heat-resist. 90°C 150°C XLPE 90°C 250°C SIR (silicone rubber) 180°C 350°C
© ABB STOTZ-KONTAKT GmbH 2CDC 002 154 N0201 | Slide 10 Correct MCB selection to protect cables Thermal aging of conductors Typical values for the thermal loading capacity are: 2.5 25 Years Material Overload Short- circuit EPR 60°C 250°C PVC 70°C 160°C PVC heat-resist. 90°C 150°C XLPE 90°C 250°C SIR (silicone rubber) 180°C 350°C
© ABB STOTZ-KONTAKT GmbH 2CDC 002 154 N0201 | Slide 11 Correct MCB selection to protect cables Protection against overload Influence of ambient conditions The current carrying capacity I z values are determined according to the tables and must be adapted for changed ambient conditions with corresponding conversion factors: Differing ambient temperatures Higher heat resistance of cable / wire Accumulation of cables / wires Higher number of loaded cores with multi-core cables and wires Wound-up wires (wire roller) As required by AS/NZS 3008
© ABB STOTZ-KONTAKT GmbH 2CDC 002 154 N0201 | Slide 11 Correct MCB selection to protect cables Protection against overload Influence of ambient conditions The current carrying capacity I z values are determined according to the tables and must be adapted for changed ambient conditions with corresponding conversion factors: Differing ambient temperatures Higher heat resistance of cable / wire Accumulation of cables / wires Higher number of loaded cores with multi-core cables and wires Wound-up wires (wire roller) As required by AS/NZS 3008
© ABB STOTZ-KONTAKT GmbH 2CDC 002 154 N0201 | Slide 12 Correct MCB selection to protect cables Protection against overload Time (s ec ) I (Amperes) Load Cable Supply ~ MCB MCB Cable Cable
© ABB STOTZ-KONTAKT GmbH 2CDC 002 154 N0201 | Slide 12 Correct MCB selection to protect cables Protection against overload Time (s ec ) I (Amperes) Load Cable Supply ~ MCB MCB Cable Cable
© ABB STOTZ-KONTAKT GmbH 2CDC 002 154 N0201 | Slide 13 Correct MCB selection to protect cables Protection against overload Time (s ec ) I (Amperes) Load Cable Supply ~ MCB MCB Cable Cable Maximum current- carrying capability before burning
© ABB STOTZ-KONTAKT GmbH 2CDC 002 154 N0201 | Slide 13 Correct MCB selection to protect cables Protection against overload Time (s ec ) I (Amperes) Load Cable Supply ~ MCB MCB Cable Cable Maximum current- carrying capability before burning
© ABB STOTZ-KONTAKT GmbH 2CDC 002 154 N0201 | Slide 14 Correct MCB selection to protect cables Protection against overload Time (s ec ) I (Amperes) Load Cable Supply ~ MCB MCB Cable Cable MCB protects the cable by tripping before the cable burns
© ABB STOTZ-KONTAKT GmbH 2CDC 002 154 N0201 | Slide 14 Correct MCB selection to protect cables Protection against overload Time (s ec ) I (Amperes) Load Cable Supply ~ MCB MCB Cable Cable MCB protects the cable by tripping before the cable burns
© ABB STOTZ-KONTAKT GmbH 2CDC 002 154 N0201 | Slide 15 Correct MCB selection to protect cables Selecting an MCB for short circuit protection of cables Let-through energy = thermal capacity of cable I f ² t = k ² S ² I f Prospective short circuit current(A) t Max. opening time of MCB (sec) k Coefficient factor of cable material S Cross section area of conductor mm²
© ABB STOTZ-KONTAKT GmbH 2CDC 002 154 N0201 | Slide 15 Correct MCB selection to protect cables Selecting an MCB for short circuit protection of cables Let-through energy = thermal capacity of cable I f ² t = k ² S ² I f Prospective short circuit current(A) t Max. opening time of MCB (sec) k Coefficient factor of cable material S Cross section area of conductor mm²
© ABB STOTZ-KONTAKT GmbH 2CDC 002 154 N0201 | Slide 16 Correct MCB selection to protect cables Selecting an MCB for short circuit protection of cables Cable Cable Supply MCB Load ~ I f 2 t = k² S² k² S² I f 2 t I b I f
© ABB STOTZ-KONTAKT GmbH 2CDC 002 154 N0201 | Slide 16 Correct MCB selection to protect cables Selecting an MCB for short circuit protection of cables Cable Cable Supply MCB Load ~ I f 2 t = k² S² k² S² I f 2 t I b I f
© ABB STOTZ-KONTAKT GmbH 2CDC 002 154 N0201 | Slide 17 Correct MCB selection to protect cables Any Questions?
© ABB STOTZ-KONTAKT GmbH 2CDC 002 154 N0201 | Slide 17 Correct MCB selection to protect cables Any Questions?